For trenchless underground pipeline and utility installations
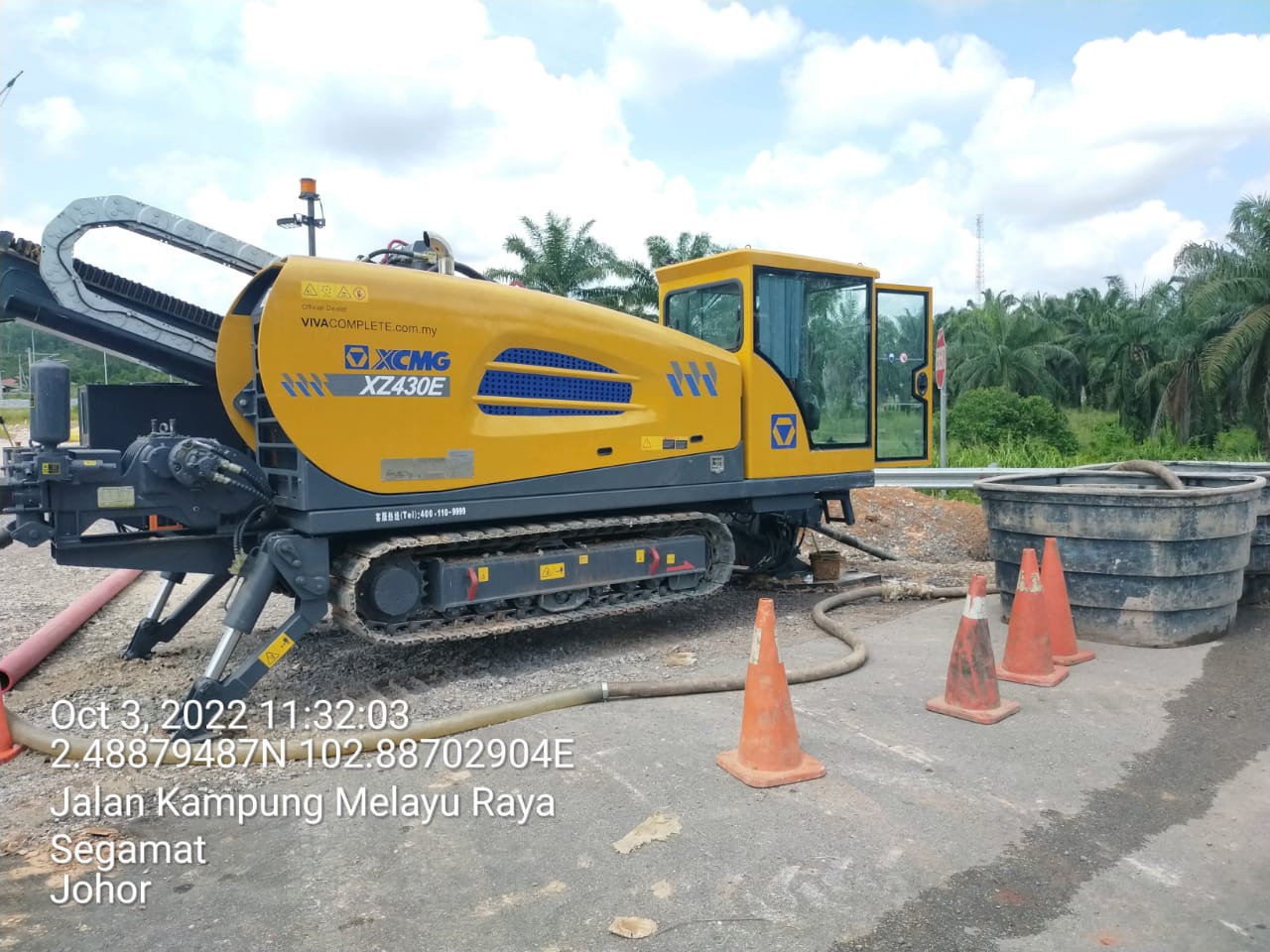
Swis is specialist in small and mid rig Horizontal Directional Drilling. Horizontal Directional Drilling (HDD) is commonly used for trenchless underground pipeline and utility installations. It is a method for crossing roads, railroads, rivers, bays, and a variety of other obstacles with precision and efficiency while minimising environmental impact. It is a guided horizontal directional boring system capable of installing ducts for utilities such as power or telecommunications cables and gases steel pipes as well. The primary application of this technology is in developed areas where surface disruption is much concern, not because of cost but also because of traffic flow and customer satisfaction.
HDD is utilised in situations that allow for an angled installation and requires sufficient space at the rig site to set up a drill pad.
HDD machinery may create tunnels ranging in diameter from 50mm to 600mm, with a typical run length between 100m and 300m, depending on soil conditions, equipment employed, and drilling depth. This system cuts with high-pressure fluid jets. These jets are equipped with carbide cutting blades to assist in breaking or penetrating more compact sediments, chalk, some shale, and up to 30% volume of rubble and gravel.
The drilling fluid consists of a combination of water, betones, and polymer. The fluid nozzle cutting of Betonies gives the power to excavate silt while leaving a lubricated tunnel for utility installation. The betonies solution is a gel-like, viscous fluid that suspends sediment particles. The fluid nozzles of the betonies will cut the sediment, but will not damage nearby materials such as concrete, metal, or plastic. Normal operating pressure for fluid nozzles is up to 1500 psi. When generating 150mm tunnels with the cutting head and rear reamer, the maximum fluid consumption is 30 litres per minute. Clay-type sediments are penetrable by the fluid jets at a pressure of 1500 psi for approximately 10 mm.
This indicates that high pressure fluid nozzle cutting is significantly distinct from water boring techniques, which utilise much larger volumes of fluids that might result in significant cavities and surface subsidence. From our operating experience, there are no surface subsidence occurred.
This method controls the course of the drilling tool based on the alignment of the nozzles and the geometry of the drilling head. At average installation depths of 1.5 metres, the drilling head equipment, in conjunction with an internal transmitter, determines the position of the tool to within 3.0 centimetres. Depending on the needs of the project and the type of silt, tunnel placement precision can be maintained at 15 cm.
We provide our clients in the construction industry, as well as those in the pipeline and utility industries, with Horizontal Directional Drilling services across Peninsular Malaysia and East Malaysia. Our company serves the Malaysian market and has vast experience in Telecommunications and Power line.
HDD Method
If an HDD is deemed feasible, a drill path is planned to fulfil the criteria of the crossing, and entrance and exit points for the drill are determined. Before determining the site of the drill entrance point, the width and depth of the river or stream are measured. Depending on the depth of the river or stream, the drill entrance point is positioned a minimum of 5 metres from the river bank or edge of the stream, with a 1.5-meter clearance under the river bed and a maximum tilt angle of 12 degrees from the horizontal. On Pre-site Planning we will ensure the Utility Mapping and detection of utilities is done. This is include with send notification to utilities company, site visit with utilities company to ensure there is no utilities at proposed drilling area.
During the pre-site planning phase, the location for the drill entrance was selected, and the HDD drill rig and other supporting equipment were then set up there. Along the trajectory of the chosen drill hole, a pilot hole is drilled. At a convenient place, a small opening called a “start pit” is dug. The drilling tool is then hooked to the drill rods and progressed into the ground to a target pit where the utility cables or pipelines will be pulled.
Then, betonite is expelled from nozzles into the drill and driven through the ground to make a pilot hole. The drill head contains a transmitter that allows the operator to locate the drill head within a 3cm tolerance. With a two-way radio, the operator can provide commands to drive the drill head along the specified drill path, providing him or her complete control.
The drill head can be directed in any direction, including straight ahead, to the left, to the right, up and down.
The horizontal and vertical coordinates along the pilot hole in relation to the initial entry point are determined using periodic readings from a probe that is situated close to the drill bit. The path of the pilot hole can also be tracked using a surface monitoring system that determines the location of the down hole probe by taking measurements from a surface point.
After breaking the ground surface at the exit site, the down-hole assembly is removed from the drill and replaced with a back reamer. This allows the drill to continue drilling. While the drill is brought back through the bore hole, a back reamer increases the diameter of the drill hole that has been created. The back reamer is equipped with a set of nozzles that provide sufficient mud flow and pressure to cut and remove dirt, therefore enlarging the pilot hole to the desired diameter. The diameter of a cable or conduit can range from 50mm to 600mm. The drill rods will continue to revolve and retract while being pulled along the utility cable, and the product will be inserted simultaneously without stress.
On the exit side of the bore hole, a pipe that is then attached is slightly longer than the length of the drill that was used to create the hole. The pipe is dragged into the exit hole, and the process of pulling it back into the bore hole is repeated until the entire pipe is inside the bore hole. After the pipe has been successfully pulled back, the drilling equipment is then disassembled and stored away until it is needed again. After that, this pipe is joined to the pipe that was laid down in the normal manner, and the work areas are then reinstated.
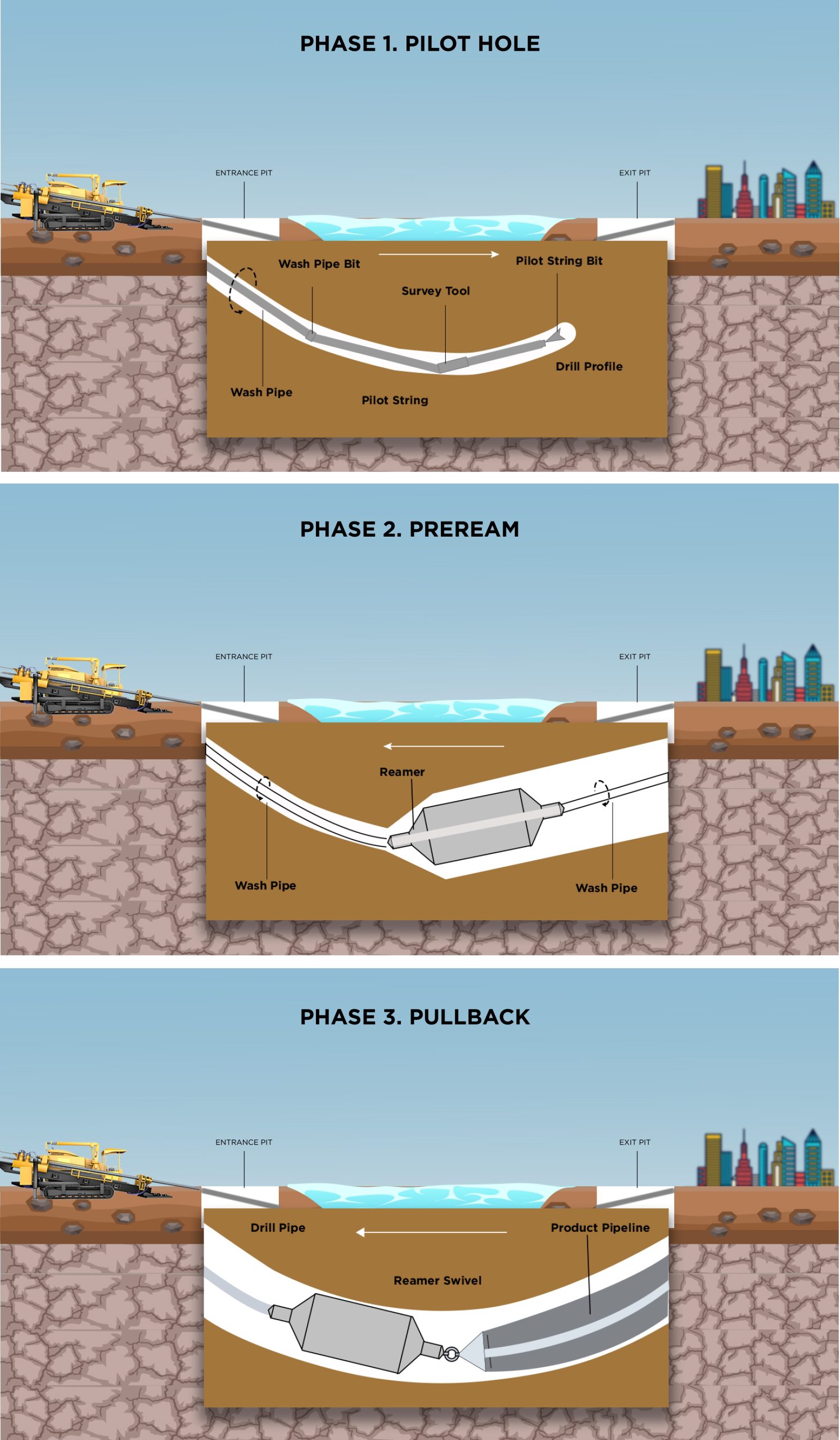